Selecting the optimal binding machine is a pivotal decision for any business involved in book production or similar ventures. The right machine can significantly enhance efficiency, quality, and overall profitability. However, choosing a binding machine can be a challenge, especially when there are several factors to consider. Mistakes during the selection process can lead to increased costs, inefficiencies, and production delays. In this guide, we will outline 8 critical mistakes to avoid when choosing a binding machine and offer practical solutions to help you make the right choice.
Importance of Using Binding Machines
Binding machines have revolutionized the book production industry, offering unparalleled efficiency, precision, and versatility. They streamline the process of organizing papers into bound books, making them ideal for companies that frequently handle large volumes of documents, such as reports, proposals, or manuals. From softcover binding to hardcover binding, binding machines cater to a wide range of book formats and production volumes. By choosing a binding machine which is reliable, businesses can streamline their operations, improve turnaround times, and elevate the overall quality of their products.
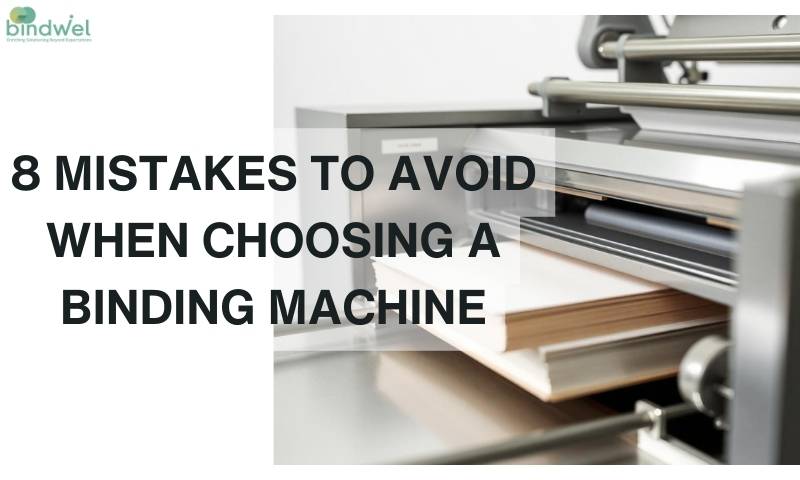
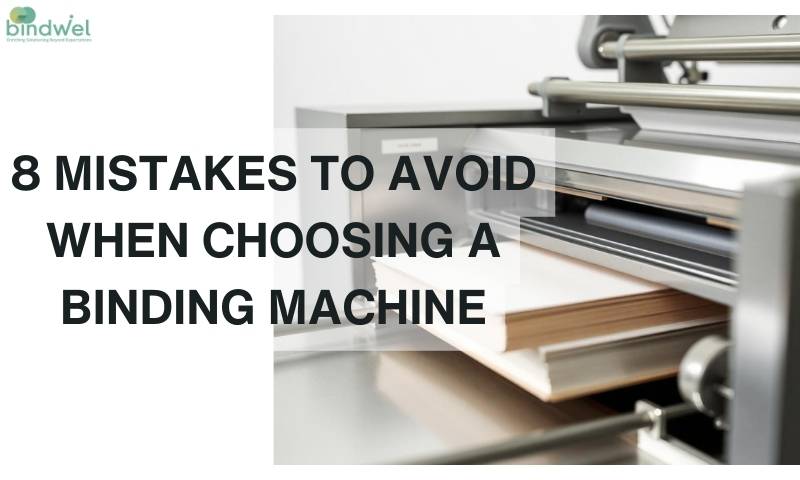
Mistakes to Avoid While Choosing a Binding Machine
1. Underestimating the Importance of After-Sales Support
Mistake: Overlooking the necessity of robust after-sales service and technical support can lead to operational downtime and costly repairs.
Solution: After-sales support is often an undervalued aspect when purchasing equipment like a bookbinding machine. Issues such as mechanical failures or software glitches can halt your operations, especially if you don’t have immediate access to technical assistance. Before making a purchase, ensure the manufacturer offers timely support, including troubleshooting guides, spare parts availability, and warranty services. A reliable after-sales service can help mitigate downtime, ensuring your business operations run smoothly.
2. Ignoring the Importance of Machine Durability for Long-Term Use
Mistake: Opting for a cheaper machine without considering long-term durability and maintenance costs.
Solution: A common mistake while choosing a binding machine is focusing too much on price rather than long-term value. While a low-cost machine may seem like an economical choice, it may not withstand heavy use over time. Machines made with inferior components often break down sooner and require frequent repairs. Instead, prioritize durability when choosing a binding machine. Opt for machines constructed with high-quality materials that can endure continuous use, even if the initial cost is higher. This approach will save you money in the long run by reducing repair and replacement costs.
3. Focusing Only on Current Production Volumes
Mistake: Buying a machine based solely on current production needs without accounting for future growth.
Solution: Another major mistake businesses make is not planning for future expansion. Your current production volumes may be manageable with a basic binding machine, but what happens as your business grows? Investing in a machine with the capacity to handle increased volumes ensures that you won’t outgrow your equipment too quickly. A scalable machine with adjustable features will allow you to meet higher demands as your business evolves, preventing the need for frequent upgrades.
4. Choosing a Binding Machine Based Solely on Initial Cost
Mistake: Prioritizing lower upfront costs without considering the total cost of ownership.
Solution: Initial cost is certainly a factor when deciding to buy a binding machine, but it’s critical to consider the total cost of ownership. Cheaper machines may have hidden costs, such as higher energy consumption, increased maintenance, or a shorter lifespan. When you choosing a binding machine, factor in ongoing costs like energy efficiency, required supplies, and potential repairs. Opt for a model that offers the best long-term value, even if it means a slightly higher upfront investment.
5. Not Evaluating Energy Efficiency
Mistake: Overlooking energy consumption, which can increase operational costs, especially in continuous production environments.
Solution: Continuous production environments demand machines that are not only efficient but also cost-effective in terms of energy consumption. A binding machine that consumes excessive energy can lead to increased utility bills over time, making operations less sustainable. When evaluating different models, check the machine’s energy efficiency rating. Opting for energy-efficient machines reduces operational costs, helps your business meet sustainability goals, and minimizes environmental footprint.
6. Failing to Test Machines in Real-World Conditions
Mistake: Relying solely on product demo videos or brochures without testing the machine under your specific production conditions.
Solution: Every production environment has unique variables, from document types to production speed and operator experience. Product demonstration videos and brochures may not give you an accurate understanding of how a machine will perform under your conditions. Before purchasing, visit a vendor’s facility to evaluate the machine’s performance firsthand. This will allow you to test the machine under real-world conditions, ensuring that it meets your business’s requirements.
7. Not Accounting for Operator Training Needs
Mistake: Purchasing complex machinery without considering the training required for operators.
Solution: Even the most advanced binding machines can become bottlenecks if operators aren’t adequately trained to use them. Complex machines often have multiple features and settings that require specialized knowledge to operate efficiently. Ensure that your manufacturer provides training and resources to help your team become proficient with the new equipment. Investing in training up front can prevent costly mistakes and reduce downtime associated with operator errors.
8. Overlooking Workspace and Workflow Requirements
Mistake: Failing to consider the machine’s footprint and how it fits into your existing workspace and workflow.
Solution: It’s easy to forget about the physical space a binding machine occupies. A machine that is too large for your workspace or poorly integrated into your workflow can create inefficiencies and slow down production. Before purchasing, measure the available space and visualize how the machine will fit into your existing processes. Ensure there’s enough room for operators to work comfortably and for the machine to be easily accessible for maintenance. Proper planning will help maintain an organized, productive workspace.
How to Choose The Best Binding Machine for Your Requirement
Selecting the best binding machine for your business depends on several factors, including production volume, book format, desired output quality, budget constraints, and available workspace. Here’s how to approach the decision-making process:
- Understand Your Binding Volume: Calculate how many documents you need to bind daily, weekly, or monthly. High-volume binding tasks require more robust machines.
- Discover your Book Format: Ascertain the type of binding required for your books, such as perfect binding, saddle stitching, or hardcover binding.
- Ensure Book Quality Meets Expectations: Evaluate the machine’s capabilities to ensure it meets your desired standards for book appearance and durability.
- Assess Durability and Maintenance Needs: While a less expensive machine may save you money upfront, higher-quality machines tend to be more reliable and require less maintenance over time.
- Check for Future Scalability: Ensure that the machine you select can accommodate future growth. Businesses evolve, and so do their binding needs.
- Evaluate Training Requirements: Complex machines may require operator training. Factor this into your decision to avoid delays in implementation.
Wrapping Up: The Ultimate Guide to Choosing the Best Binding Machine
Choosing the right binding machine is a crucial investment for any business that regularly produces bound documents. Avoiding common bookbinding mistakes like underestimating future production needs, ignoring after-sales support, and neglecting machine durability can save your business time and money. By considering factors such as operator training, energy efficiency, and workspace requirements, you’ll make an informed decision that enhances productivity and delivers long-term value. With the right machine in place, your business can streamline document production, reduce operational costs, and produce high-quality, professional results. Remember, a well-chosen binding machine is an investment that will pay dividends for years to come.
Ready to make the right choice for your binding needs?
Explore our range of high-quality binding machines and take your business to the next level. Contact us today to get started!
👉 Follow Bindwel journey on social media for more inspiring success stories and bookbinding innovations! Stay ahead of the curve in the world of bookbinding! Follow Bindwel on Facebook, LinkedIn, Twitter, Instagram and YouTube for the latest industry updates, innovative solutions, and expert tips to optimize your production.
#BindingMachines #BookBinding #BusinessEfficiency #MachineDurability #AfterSalesSupport #ProductionVolume #EnergyEfficiency #OperatorTraining #BindingSolutions #BindingMistakes #ChoosingABindingMachine #ProductionTips #Bindwel